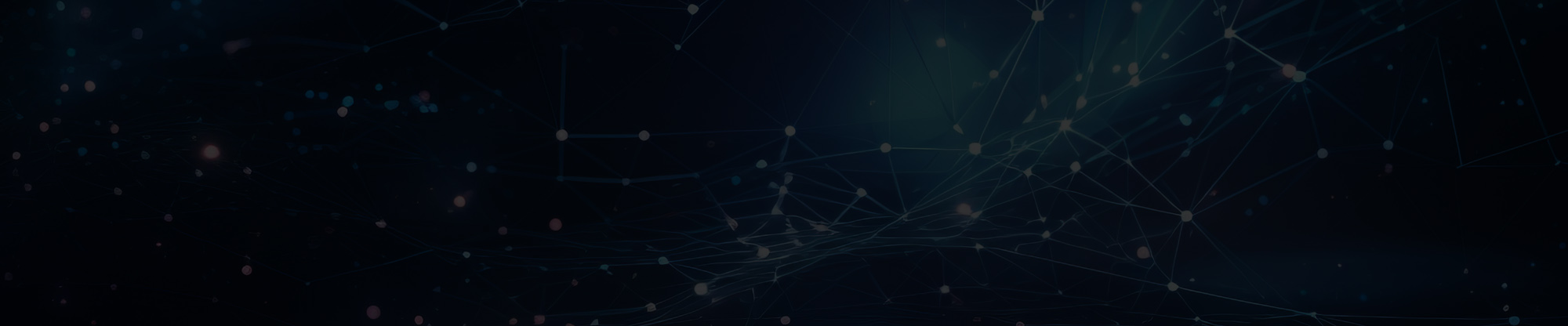
Arachnoforce's haptic device uses a wire-driven system to display force.
It is composed of a wire, a pulley, and a DC motor.
It can realize extremely accurate force sense presentation.

Principle of wire-driven haptic presentation

The wire-driven haptic device can adjust the degree of freedom for position detection and force display by changing the number of wires. In addition, the workspace for force display can be changed arbitrarily by simply changing the arrangement of the motors, which allows for high scalability from desktop environments to human scale.
Extremely low inertia
Force sense presentation devices have the characteristic that unless the inertia and viscosity of the end effector are sufficiently reduced,
it becomes difficult to correctly present the output force.
Therefore, the inertia of the end effector must be as low as possible.
Wire-driven Haptic device connect the motor and end effector with lightweight wires, so
it is possible to minimize the inertia of the end effector.
The ability to operate in free space as if you had nothing is called transparency.
Arachnoforce's Haptic device achieves high transparency.
End effector stiffness
Link-driven haptic devices have difficulty displaying hard surfaces because it is difficult to increase the rigidity of the end effector. Some devices have increased the rigidity of the end effector by using a parallel link mechanism, but this increases the inertia of the end effector and impairs the natural operability of the device. Wire-driven haptic devices have a parallel structure using multiple wires, which makes it possible to increase the rigidity of the end effector, and furthermore, our unique high-resolution haptic rendering technology makes it possible to display hard surfaces such as metal surfaces.
Wearable haptic device
The commercialization of high-performance, cost-effective Head Mounted Displays (HMDs) is creating an environment
in which people can experience highly immersive VR/AR worlds.
As a result, the potential for related business and gaming applications is rapidly growing.
A haptic device designed to be used in conjunction with an HMD must have a structure that allows the user to move
around freely without the restrictions of the device.
Then, it is necessary to present the force to the part where you can experience the presence and reality of the object.
In addition, the price must be commensurate with the price of HMDs, which have excellent cost performance in recent years.
Conventional haptic devices are stationary, so they are limited to use in a fixed position, which limits the user's movements.
Furthermore, because of the mechanical link drive method, the device is heavy and puts a heavy burden on the user
when wearing the device, greatly inhibiting the sense of realism.
Also, compared to HMDs that have excellent cost performance in recent years, they are extremely expensive.
Composed of lightweight parts, SPIDAR-W achieves wearability that other devices cannot achieve.
It is a highly accessible device that can be easily installed.
Weighing only 880g, it can be used for long periods of time without fatigue.
Using the shoulder as a fulcrum, force can be applied to the upper arm and forearm,
allowing you to strongly experience the presence and reality of objects.